Alexander Dennis Limited (ADL) opened its Singapore facility on 20th September 2018, located at Woodlands Spectrum 1. The new facility is the regional office and aftermarket support for Asia, and contains a parts warehouse, bus workshop, training room, and offices. It is also designed to support contract requirements defined by the Land Transport Authority (LTA).
As part of the opening ceremony, in addition to the Enviro500 3 Door concept bus, an Enviro500 bus chassis was shipped in for the event. This particular unit is a Euro 6, 12-metre, right-hand drive Alexander Dennis Enviro500 MMC bound for New World First Bus in Hong Kong. The bus operator already owns Enviro500 and Enviro500 MMC buses in its fleet.
The bus is part of a batch of 90 Euro 6, 12-metre, 3-axle double-deck buses ordered tendered by Citybus and New World First Bus in March 2017 [Link], for which ADL was awarded the contract.
For the Asia Pacific market, ADL manufactures its chassis at Pasir Gudang in Johor Bahru, Malaysia. This chassis was shipped out shortly after the opening ceremony and bound for ADL’s assembly plant in Zhuhai., China.
The chassis presented here (VIN: SFD4ADNR6JMTL6515) was registered to New World First Bus on 11 December 2018 as VW9946 (fleet code 5782).
Background
The Enviro500 MMC chassis was launched in 2012, having been redesigned from the initial Enviro500 launched in 2002. It is the latest design iteration of the Enviro500 product offered by Alexander Dennis Limited (ADL), as of 2018. The chassis featured improved maintainability, reliability, lightweight body, and reduced operating costs with low life-cycle cost.
New design features included offsetting the longitudinally-mounted engine and gearbox, along with a safer straight staircase and fuel tank underneath the stairs, a design feature adapted from the Enviro400. The chassis was offered in lengths between 11.3m and 12.8m. A rear-axle steering (RAS) system is also made available, supplied by ZF (Servocom® RAS).
In Hong Kong, the Enviro500 MMC product is extremely popular, with over 3,000 units delivered to franchised bus operators Kowloon Motor Bus (KMB), Citybus (CTB) and New World First Bus (NWFB) as of September 2018. Among these operators, KMB owns the most buses (with nearly 2,000 units), and smaller operators like Long Win Bus and MTR Bus also operate the Enviro500 MMC.
In Singapore, 216 units of the Enviro500 MMC operate on the roads. An initial 201 was purchased by SMRT and entered service in 2014, with some units transferred to other operators as part of the Bus Contracting Model (BCM). A subsequent 15 units ordered by the Land Transport Authority (LTA) entered service in 2017. A 3-Door concept bus was also built for static display.
For the Asia-Pacific Market, ADL manufactures its chassis at Pasir Gudang in Johor Bahru, Malaysia, through a partnership with Terberg Tractors Malaysia Sdn Bhd (TTM), a subsidiary of Sime Darby Industrial. The facility produces various types of ADL chassis, most of which are shipped to its main assembly plant in Zhuhai, China. Zhuhai Granton Bus And Coach Co., Ltd. (珠海市廣通汽車有限公司) has officially been in partnership with Alexander Dennis Ltd since 2011 and supplies the region with ADL buses, including all Enviro500 buses operating in Singapore.
The Enviro500 MMC is also known as the Enviro500NG (for New Generation), Trident E500 Turbo, or simply E50D (with ‘D’ indicating diesel) or E50H (with ‘H’ for hybrid). The Hybrid variant was made available in 2013, incorporating a series hybrid drive-train by BAE Systems (HybriDrive series-E), achieving the Euro VI emission standard.
Overview
This article will provide a very basic introduction to the main subsystems of a bus, with accompanying photos of its chassis, and (hopefully) and appreciation of the complex mechanisms behind a modern bus. Many of these components and vehicle subsystems are similar between buses from manufacturers from a technical standpoint but differ in their layout.
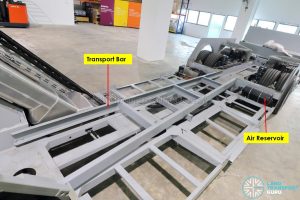
The bus chassis is the base structure for which the Enviro500 bus is built. Alexander Dennis offers the Enviro500 product as a complete bus, or as a standalone chassis. Due to the positioning of the engine and transmission on the left, the bare chassis naturally tilts slightly to the left.
The ladder-like structure in the middle of the chassis is referred to as a Transport Bar, which offers rigidity during transportation of the chassis. It would be removed once the chassis arrives at the bodybuilder factory for body assembly. More components will be explained in the following sections.
Engine & Transmission Components
Engine | Cummins L9E6C340B (Euro 6) Inline 6-cylinder turbocharged, 8849cc displacement Power/Torque rating of 340 hp (254 kW) @ 2100 rpm / 1526 Nm @ 1400 rpm [1] |
Emission Standard | Euro VI-compliant Modular Aftertreatment System utilizing Selective Catalytic Reduction (SCR), hence requiring diesel exhaust fluids (AdBlue). The modular system combines a Diesel Particulate Filter (DPF)/Diesel Oxidation Catalyst (DOC) and Selective Catalytic Reduction (SCR) chamber. Meets the latest Euro VI emission standard. |
Transmission | ZF EcoLife 6AP1700B Six-speed automatic transmission with integral hydrodynamic retarder |
The Euro 6 ADL E500 MMC is fitted with a Cummins L9 powerplant, supplied by American corporation Cummins Inc., which specialises in engine manufacturing (exact model: L9E6C340B). The inline six-cylinder engine has a displacement of 8849 cc, and delivers a power rating of 340 hp (254 kW) @ 2100 rpm, and torque rating of 1526 Nm @ 1400 rpm.
The Cummins L9 engine installed on this chassis is an updated 2019 type, which differs from the 2017 type previously offered for city buses. For the Hong Kong market, this means that the newer engine differs from that installed on the first two Euro 6 ADL E500MMC buses delivered to Kowloon Motor Bus in late 2017 (Fleet code: E6T1 and E6T2), which were also the first two Euro 6 Enviro500 buses in Hong Kong (and were rated at 330hp). Existing Euro 6 Enviro500 buses in Citybus’ and New World First Bus’ fleet, delivered from 2018 onwards, are of the 2019 type.
Since the 2019-type engine is also marketed as a nonroad engine*, it is compliant with Stage V emission standards set by the European Union for non-road mobile machinery. The Cummins L9 also replaces the Cummins ISL engines used on older Enviro500 and Enviro500 MMC buses.
* = Nonroad engines are used in non-road mobile machinery (NRMM), such as generators, bulldozers, pumps, and construction machinery. These equipment require a combustion engine, but are not intended for carrying passengers or goods on the road.
Cummins offers emissions control via its Modular Aftertreatment System, which is explained in a later section.
Another upgrade for the Euro 6 engine such as the Cummins L9 is the use of a Variable Geometry Turbocharger (VGT), which offers turbo performance and driveability improvements across the entire range of engine speeds while also acting as an exhaust brake. In contrast, the Cummins ISLe used on Enviro500 buses up to Euro 5 have a wastegated turbocharger with a lower rpm operating range. The difference is somewhat audible, with the Euro 6 engine generally having a softer turbo noise.
New World First Bus has also opted for the Oilmaster automatic oil level control system, supplied by Dutch company Groeneveld. It ensures that the oil in the engine is always at the optimal level by monitoring oil levels in the engine sump and replenishing where necessary, eliminating the need to manually check oil levels at regular intervals. The main tank is the translucent plastic piece at the bottom, while the upper housing conceals the pump unit. Singapore’s Volvo B5LH buses also feature this.
In Singapore, Bus Captains are required to check oil levels manually before the start of their shift, using a dipstick.
For the transmission, the bus is fitted with the ZF EcoLife 6AP1700B gearbox supplied by ZF Friedrichshafen AG, a German company focusing on driveline and chassis technology. The transmission unit offers six gears forward and one in reverse, with a gear ratio spread of 7.40 – 0.62 (forwards) and 4.23 (reverse). It is also integrated with a hydrodynamic retarder for efficient braking at high speeds.
The ZF EcoLife 6AP1700B transmission is a very popular pairing with the Enviro500 MMC chassis, with the other being the four-speed Voith DIWA 864.5.
- [1] Cummins L9 (Stage V) for 2019 – Cummins
- [2] Stage V – Technology That Transforms Leaflet – Cummins [PDF]
- [3] Smart Efficiency.™ – Engines For Urban Transit And Shuttle Applications – Cummins [PDF]
- [4] Product Overview – ZF [PDF]
- [5] Oilmaster – Groeneveld Lubrication Solutions
Fuel System
For the fuel system, the Enviro500 is fitted with a single 350-litre aluminium fuel tank mounted above the right front axle of the bus, and underneath the staircase of the completed double-deck bus (after body assembly). It is designed to be lightweight and offers more than the adequate range for a day’s worth of revenue service.
The chassis is equipped with the Posi/Lock 105 fuelling system supplied by Emco Wheaton. Commonly used by fleet operators in Hong Kong and abroad, the system offers high-speed fueling (between 75 to 185 litres per min). A special refuelling nozzle that locks onto the grooves of the fuel adapter (seen in gold) is used, resulting in no spillage. Fuel flow is automatically stopped when the fuel tank is 95% full.
Underneath the metal cap, the diesel system is sealed by a spring-loaded polypropylene piece that prevents vandalism by introducing foreign materials or liquids into the nozzle or fuel tank of the bus.
At the back, we see the fuel sensor, level control valve, and pressure relief valve.
- The Level Control Valve bleeds air out of the fuel tank whilst refuelling is in progress, and also monitors the fuel level within the tank. At approximately 95% full, the Level Control Valve closes. In turn, the refuelling nozzle automatically shuts off when it senses the back-pressure in the fuel tank.
- The Pressure Relief Valve protects the fuel tank in the event of a fire, meeting US DOT standards for fuel tank protection in a fire situation
- The Fuel Sensor is supplied by Fozmula and communicates low fuel warnings to the driver’s cab.
Fuel is then fed to the engine through fuel lines running down the length of the bus. The fuel filter (located within the engine bay) screens out dirt and rust particles from the fuel before it is fed into the combustion engine.
AdBlue System
For emissions control, the bus utilizes Selective Catalytic Reduction (SCR) to reduce nitrogen oxide (NOx) emissions, converting them into atmospheric nitrogen and water vapour through using diesel exhaust fluids (such as AdBlue) as a catalyst. AdBlue is a 32.5% high-purity urea solution diluted in deionized water, and is injected upstream of the SCR catalyst.
AdBlue is stored in a small tank at the right side of the bus, just ahead of the drive axle (middle axle). It has a capacity of 34 litres (of which only 22.8 litres are usable). The AdBlue system uses Bosch’s Denoxtronic 2.2 exhaust gas treatment system specifically developed for heavy vehicles. The supply module can be seen beside the right rear tyre, but will be concealed by bodywork panels after bodywork assembly. The unit pumps AdBlue fluid from the tank and pressurizes it for injection into the Cummins exhaust aftertreatment system.
Cummins offers emissions control via its Modular Aftertreatment System, which removes emissions entirely by passive regeneration with no impact on equipment operation. The modular system combines a Diesel Particulate Filter (DPF)/Diesel Oxidation Catalyst (DOC) and a Selective Catalytic Reduction (SCR). As such, it meets the latest Euro VI emission standard, without the need for Exhaust Gas Recirculation (EGR) used on other Euro VI bus models.
Exhaust from the engine is first passed through a (1) Diesel Oxidation Catalyst and (2) Diesel Particulate Filter, housed within the same unit, with removes 99 per cent of Particulate Matter (PM) soot from the exhaust system. Next, the (3) Urea Dosing System injects atomized urea (AdBlue) into the exhaust system, and the (4) Decomposition Reactor hydrolizes the DEF, releasing ammonia gas and mixes it with the exhaust gas. Finally, the (5) Selective Catalytic Reduction (SCR) System reacts with nitrogen oxides over a catalyst to form harmless nitrogen gas and water.
Do check out the Selective Catalytic Reduction (SCR) article for more details about the SCR process.
- [1] AdBlue® – Yara
- [2] Modular Aftertreatment System – Cummins [PDF]
- [3] Denoxtronic exhaust gas treatment system – Bosch (& Brochure[PDF])
Pneumatic Systems & Peripherals
On the ADL Enviro500, compressed air (pneumatic) systems are used to operate several systems, such as the service brakes, parking brake, suspension, and doors. The compressed air system itself comprises many complex sub-components, but can be simplified as follows:
The compressed air systems on the ADL Enviro500 are supplied by Knorr-Bremse, a German company specialising in braking systems for rail and road vehicles. Firstly, air is compressed by the engine-driven Air Compressor mounted at the lower right of the engine. The ADL Enviro500 uses a twin-cylinder, 630cm3 air compressor.
When air is quickly compressed, it increases in temperature and needs to be cooled before being fed into the system. For that, it passes through a cooling coil within the radiator unit (on the right of the engine), where heat exchange takes place. After being cooled, air is channelled to the air processing unit (APU) for filtration to remove moistures and impurities. The APU is located beside the AdBlue tank, and ensures that clean and dry air is supplied to the pneumatic systems.
The bus has a total of four independent pneumatic systems, for the service brake, parking brake, suspension, and auxiliary. Within the pneumatic system, compressed air is stored in a supply reservoir located under the driver’s cabin, with one reservoir for each pneumatic system (a fifth backup reservoir is located on the left side of the bus). The following sections will discuss the individual subsystems which rely on compressed air.
Braking systems
The ADL Enviro500 uses full a full air system with Electronic Brake System (EBS) supplied by Knorr-Bremse, which includes an antilock braking system (ABS) and antislip regulation (ASR) for anti-lock braking and traction control respectively. The EBS integrates the basic functions of braking control, ABS and ASR, into one electronic system.
While the vehicle has only one set of disc brakes, they are controlled by two separate pneumatic circuits; the service brake circuits and the parking brake circuit, which operate on different principles. Firstly, the service brake is applied through the brake pedal-controlled air valve, which supplies air pressure from the reservoir to the brake chambers at each wheel when the brakes are applied. The air pressure supplied through the brake application valve is proportional to valve movement, and thus the degree of brake application by the bus driver.
For the parking brake mechanism, the brakes are held on by powerful springs when the system is unpressurized. For the bus to move off, air pressure is used to compress the springs and release the brakes, allowing the vehicle to move off. When the handbrake is applied, air pressure is bled and the springs extend, re-engaging the brakes. On the Enviro500, the handbrake is active on the drive axle only.
Heavy vehicles use air brakes as it offers several advantages over hydraulic brakes which are used on lighter vehicles such as automobiles.
Suspension system
The Enviro500 uses an air suspension system with a front kneeling feature which allows for a step height of as low as 250mm.
Doors
Door systems use compressed air from the auxiliary air system.
- [1] Electronic Systems – Knorr Bremse
- [2] ZB44 Air Processing Unit – Knorr Bremse
- [3] Air Brake Service System – The Car Tech
- [4] Parking Brake – Wikipedia
Next Page (Page 2):
- Axle, Steering & Hydraulic Systems
- Electrical Systems
- Cooling Package & Miscellaneous
- Photo Gallery